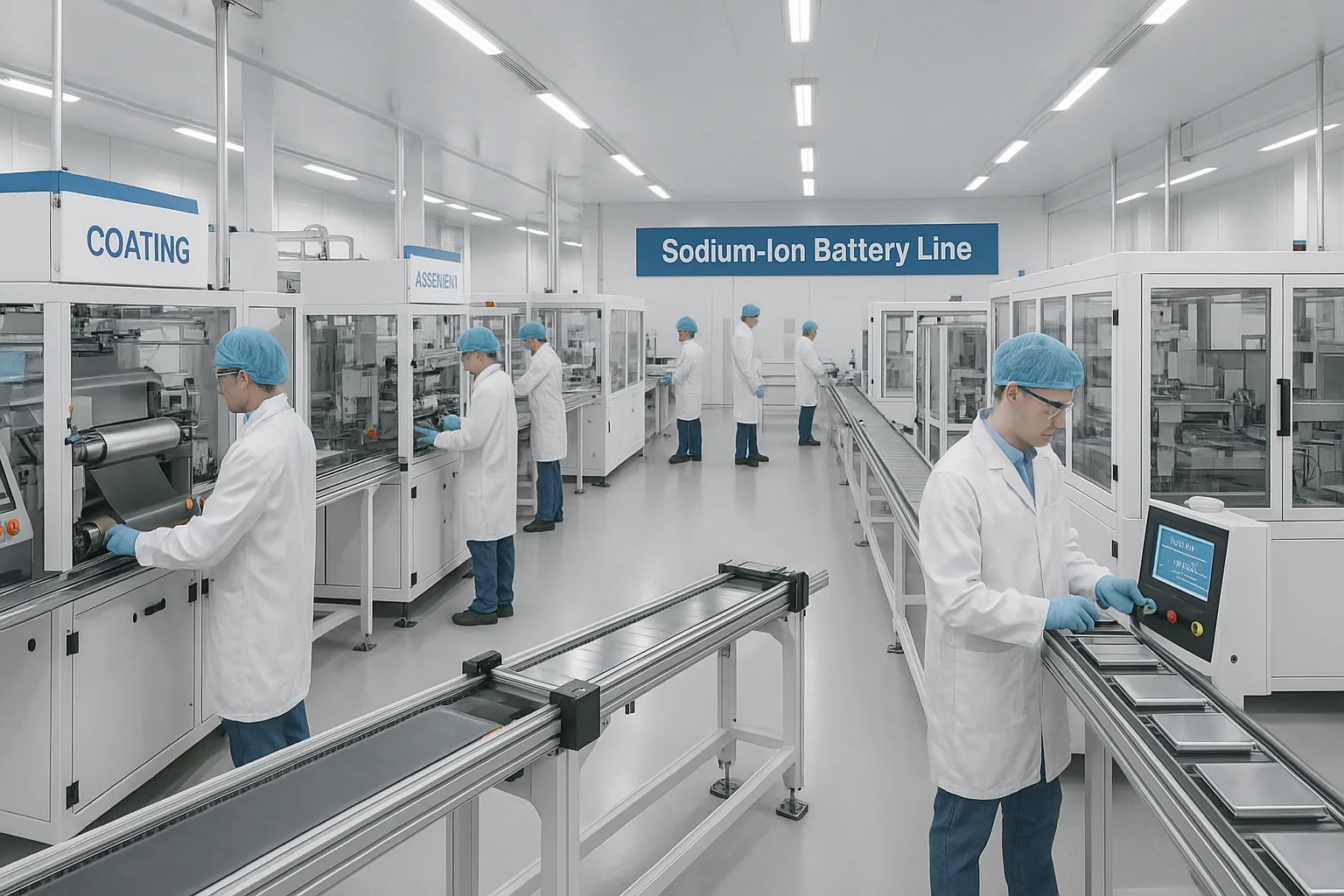
Curious about how sodium-ion batteries are produced? You’re not alone—as these batteries gain traction, understanding their manufacturing becomes increasingly important.
Sodium-ion batteries are manufactured using processes similar to lithium-ion batteries, involving electrode slurry preparation, coating onto current collectors, drying, calendaring, assembling into cells, electrolyte filling, and final sealing.
Having closely followed battery production methods, I find the similarities and differences fascinating—let’s explore them clearly.
What Is the Manufacturing Process of Sodium-Ion Batteries?
Want to understand step-by-step how sodium-ion batteries are made?
The manufacturing process includes electrode slurry mixing1, electrode coating, drying, calendaring, electrode cutting, stacking or winding into cells, electrolyte injection, sealing, formation cycling2, and quality testing3.
Step-by-Step Manufacturing Process
Here’s a detailed breakdown:
- Slurry Mixing: Cathode/anode active materials mixed with binders and solvents.
- Coating: Slurry applied onto aluminum (cathode) and copper (anode) current collectors.
- Drying & Calendaring: Coated electrodes dried and compressed for uniform thickness.
- Cutting & Cell Assembly: Electrodes cut, stacked or wound, with separators placed between.
- Electrolyte Injection & Sealing: Liquid electrolyte injected into cell and securely sealed.
- Formation & Testing: Cells undergo charge/discharge cycling for quality assurance.
Manufacturing Stage | Purpose |
---|---|
Electrode Preparation | Uniform active material distribution |
Cell Assembly | Proper internal structure and safety |
Electrolyte Filling | Enables ion movement |
Formation & Testing | Ensures performance and reliability |
This structured approach guarantees high-quality sodium-ion cells.
What Raw Materials Are Used in Sodium-Ion Battery Production?
Interested in knowing exactly what goes into a sodium-ion battery?
Key raw materials include sodium-based cathodes4 (layered metal oxides or polyanionic compounds like NaFePO₄), hard carbon anodes5, sodium salt electrolytes6 (NaPF₆), organic solvents, separators (polypropylene or polyethylene), aluminum foil, and copper foil.
Raw Materials Overview
Here’s a concise summary:
- Cathodes: Sodium layered oxides (NaNiMnO₂) or sodium iron phosphate (NaFePO₄).
- Anodes: Hard carbon derived from biomass or petroleum-based precursors.
- Electrolytes: Sodium salts (NaPF₆) in organic solvents (EC, DEC).
- Separators & Collectors: Polymer separators, aluminum (cathode), copper (anode) foils.
Component | Typical Materials |
---|---|
Cathode | NaFePO₄, NaNiMnO₂ |
Anode | Hard carbon |
Electrolyte | NaPF₆ dissolved in EC/DEC solvents |
Current Collectors | Aluminum (cathode), Copper (anode) |
These abundant materials support sustainability7 and affordability.
Is There a Stable Global Supply Chain for Sodium-Ion Batteries?
Wondering if the sodium-ion battery supply chain is reliable?
Currently, the global supply chain8 for sodium-ion batteries is emerging but not yet fully stable or mature. Limited producers, developing material suppliers, and early-stage commercialization pose challenges to large-scale supply reliability.
Current Supply Chain Status
Here are key factors impacting stability:
- Limited Suppliers: Few companies currently produce sodium-ion specific materials.
- Scaling Challenges: Early-stage production means supply fluctuations.
- Regional Concentration: Predominantly China-based production, limited diversification globally.
Supply Chain Issue | Current Impact | Potential Solutions |
---|---|---|
Few global suppliers | Limited production capacity | Expansion and investment |
Immature logistics | Delays, higher costs | Infrastructure development |
Material availability | Restricted sourcing options | Diversified global partnerships |
Increasing demand is rapidly motivating the development of a stronger supply chain.
What Role Do Gigafactories Play in Sodium-Ion Battery Production?
Considering the impact of gigafactories9 on sodium-ion battery scale-up?
Gigafactories play a critical role in sodium-ion battery production by enabling large-scale, automated manufacturing. They significantly reduce costs through economies of scale, streamline supply chains, and accelerate global commercialization efforts10.
Importance of Gigafactories
Here’s how gigafactories contribute:
- Large-scale Production: Vastly increased manufacturing volumes lower per-unit costs.
- Automation and Efficiency: Highly automated processes enhance product quality and consistency.
- Supply Chain Integration: Centralized sourcing simplifies logistics, reduces overhead.
Gigafactory Advantage | Benefit to Sodium-Ion Production |
---|---|
Mass Production | Lower costs, affordable batteries |
High Automation | Improved quality, fewer defects |
Supply Chain Centralization | Better resource management |
Gigafactories are essential to transforming sodium-ion from niche technology to mainstream energy solution.
Conclusion
Manufacturing sodium-ion batteries involves similar steps to lithium-ion but uses distinct, abundant materials. With expanding gigafactory production and developing supply chains, sodium-ion technology is poised for large-scale commercial success.
-
Understanding this process is crucial for grasping how sodium-ion batteries achieve efficiency and performance. ↩
-
Explore the importance of formation cycling in ensuring the quality and reliability of sodium-ion batteries. ↩
-
Understanding quality testing methods can provide insights into the safety and performance of batteries. ↩
-
Explore the types of sodium-based cathodes to learn about their role in battery performance and sustainability. ↩
-
Discover the significance of hard carbon anodes in enhancing the energy density and longevity of sodium-ion batteries. ↩
-
Gain insights into how sodium salt electrolytes facilitate ion movement, crucial for battery efficiency. ↩
-
Discover how sodium-ion batteries promote sustainability through the use of abundant materials. ↩
-
Understanding the supply chain dynamics can help assess the future reliability of sodium-ion battery production. ↩
-
Learn how gigafactories are revolutionizing battery production and making sodium-ion technology more accessible. ↩
-
Stay informed about the latest advancements and challenges in bringing sodium-ion technology to market. ↩